今日味新深(No.89:2017/12/20)
積層造形法とは3次元CAD データーを実体化する方法であり、「立体をある軸に直交する多数の面で切断したときに生ずる薄片を積み重ねる」ことにより物体を3次元的に造形します。近年、金属を用いた積層造形法が実用化されるようになり、航空機エンジン部品、医療器具などへの適用が開始されました。
薄片を実体化して重ねて接合する積層方法には、接着、溶接など従来の接合方法が利用されています。金属材料に適用されている積層造形法は「粉末床溶融結合法」または「指向性エネルギー堆積法」であり、前者は粉末を敷きならしたシートの特定領域をレーザーや電子ビームの熱エネルギーにより選択的に溶融・結合させる積層造形法(図1)、後者は金属材料(金属粉末、溶接ワイヤなど)を供給しながらレーザー、電子ビーム等で熱エネルギーを与えて溶融・堆積させる積層造形法(図2)です。
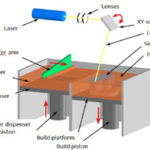
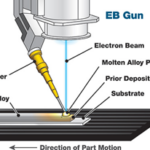
積層造形法のメリットとして、
・鍛造、鋳造では実現できない複雑形状物が作製可能
・高融点金属、鍛造が困難な材料の造形が可能
・同じ形状の製品を繰り返し製造可能
などが挙げられます。一方、デメリットとしては、
・造形に長時間が必要(特に要求精度が高くなると作製時間が増加)
・大量生産が困難
・造形物に微細孔などの欠陥が残存するため、後処理(焼鈍、HIP処理など)が必要
などが挙げられます。このような金属積層造形法は宇宙航空分野、医療分野など高付加価値製品に適用されています。航空宇宙分野では、GE社が粉末床溶融結合法によりLEAPエンジンの燃料噴射ノズル(Co-Cr合金製)を作製しています(図3)。
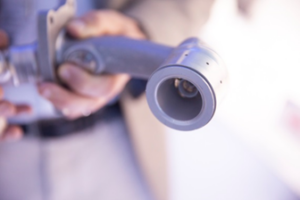
出所:GE Report 2016.2.2
URL: http://www.gereports.com/jet-engine-with-3d-printed-parts-powers-next-gen-boeing-737-max-for-the-first-time/
従来は20個の個別部品を組み立てて1個のノズルを製造していましたが、積層造形法ではノズル自体を直接造形できるため、製造コストが低減でき、信頼性が向上します。この燃料噴射ノズルを搭載したLEAPエンジンの飛行試験が始まっており、実用化に近づいています。医療材料分野では、Co-Cr 合金製の歯冠が作製されています。積層造形法では患者個人の歯の形状に歯冠を適合できるため、患者の歯に無理な力を及ぼさないという利点があります。
金属積層造形法では、従来加工法では形成不可能な複雑形状物を作製することが可能です。製造方法の制約から作製不可能であった理想的な形状を有する部品の製造が可能になることから、製品の高性能化・高付加価値化に大きく寄与する金属加工技術として注目されています。